Wood You Believe it?
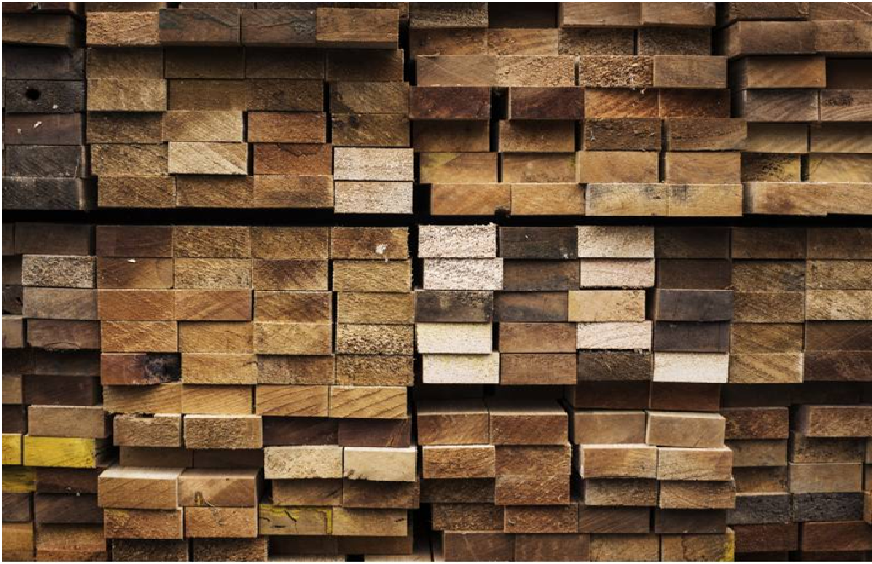
How this centuries-old material is making a comeback in 2020
The obsession begins
America’s love affair with wood started as far back as the early 1600s when the first settlers from Europe made their way across the Atlantic and settled in Virginia. The country was wild, untamed, and heavily wooded back then, so unsurprisingly, building a sturdy shelter was of utmost importance. They did so using the only material that was readily available and abundant, which is still the case across large swathes of the country. Lumber. A significant shift compared to the stuff they were used to back home in Europe, rock, brick, and limestone, these wooden houses needed to be sturdy and easy to build quickly. To their credit, they were. The lumber was easy to source, easy to transport, and easy to work with without heavy equipment or lots of muscle. And so began the tradition of building wooden homes, that for the most part, has survived to this day.
Over time, simple log cabins evolved into more traditional wooden houses that we would recognize today, made possible through advancements in framing know how. Most notably, balloon framing. With a tremendous improvement over conventional timber framing, this technique allowed towns to spring up all across America in the early 1900s. Boom towns. Houses built using this method were made faster, were far more resistant to weather, and, most importantly, were affordable to a much larger section of the growing population. These simple benefits would see wood being the dominant material used in construction for hundreds of years in the US until more modern materials such as concrete, brick, and steel worked their way into residential and commercial development.
Why Wood Endures
According to a leading market research firm, IBIS World, the wood framing market in the US is forecast to touch $15 Billion in 2020, despite a contraction of 23% expected as well. It’s essential to understand at this juncture, that this decrease has more to do with the pandemic surging across the country affecting peoples’ jobs and livelihood than an actual preference for concrete and steel homes.
What sustains this love for wood then? In a day and age when steel and concrete are readily available, surely wood must be relegated to the history books on job sites across the country.
Well, not quite.
There are more than a few reasons why wood continues to be a perennial favorite of families and contractors. Chief among them is a fit with the American lifestyle itself, which favors convenience, flexibility, and affordability over longevity.
In Europe and Asia, buildings fabricated from concrete, steel, and metal are seen as long-term investments. To be passed down within the family or retained within the business for years. By contrast, most American families and businesses prefer not to be tied down either geographically or financially, which is why wood, inexpensive in the US, is favored so heavily.
There are other reasons too, why wood is still a preferred construction material:

It’s Easier to Work With
According to IBIS World’s latest research, there are over 41,000 wood framing businesses in the US as of 2020. So, finding a skilled professional for your residential wood framing or commercial wood framing needs is not going to be a problem.
Lumber is very easy to find locally, regardless of where the job site is in the US. Having access to readily available raw materials makes a huge difference to the overall project cost and delivery schedule.
The growing popularity of prefabricated or modular construction also seems to be purpose-built for wooden structures. It’s far easier to build prefabricated wooden sections as opposed to metal or concrete ones. Changing things around once the modules are at the job site is also an option, which is literally out of the question for modules built from other materials
It’s Resilient and Tough
Certain parts of the US are prone to severe weather like Tornados, Floods, and even Wildfires. People living in these parts of the country prefer to live in homes that can easily be repaired or rebuilt. While some may argue that a building fabricated from concrete is more likely to survive a Tornado, or a Wildfire, fixing a damaged concrete wall or a metal structural pillar, for example, is most certainly going to be extremely expensive, if not downright impossible. Not the case if your house is made from wood.
New forms of engineered wood called Cross Laminated Timber or CLT have been developed that are now more resistant to warping, termites, fire, and other factors traditionally cited by wood framing naysayers. Hailed as the eco-friendly material of the future (compared to steel or concrete) despite being used for hundreds of years, beams made from this type of wood are being used to frame everything from multifamily apartment complexes to office buildings across the country.
Most importantly, despite appearances and information on the internet, most professional commercial framing contractors and construction workers prefer wood over steel and concrete as it’s a perfect choice for projects that involve other wooden components as well. For example, if the project involves creating windows or doorways, it’s better to use wooden studs instead of steel ones, as it’s easier to nail something into the door or window at a later stage.
Wooden studs or frames also have many other advantages over metal ones, since it’s a lot tougher than the manufacturers and proponents of metal framing would like you to believe. A few of these advantages are:
Wooden studs are structurally more durable than metal studs. As strange as that might sound to many, it’s 100% true. Wood is denser than metal, and as a result, can support a tremendous amount of load-bearing weight.
Wooden studs are easier to work with. Nothing beats lumber in terms of flexibility and ease of use, from physical movement around the job site to cutting it into predetermined shapes and sizes.
Wooden frames last a long time. Wood has been used in construction for centuries, and even if damaged through fire or age, can easily be replaced and repaired with minimal investment.
Modern lumber is phenomenally resistant. The usual arguments against timber, that it is susceptible to warping, insect damage, and fire are slowly disappearing with the advent of treated timber and modern construction methodologies.
It’s Earthy
Wood has a natural feel that gives the occupants of a building or a home a sense of being connected to nature. Called Biophilic Design, it is a concept gaining popularity with Architects and Design firms across the country. According to Wikipedia, it’s a way to ‘increase occupant connectivity to the natural environment through direct nature, indirect nature, and space & place conditions.’
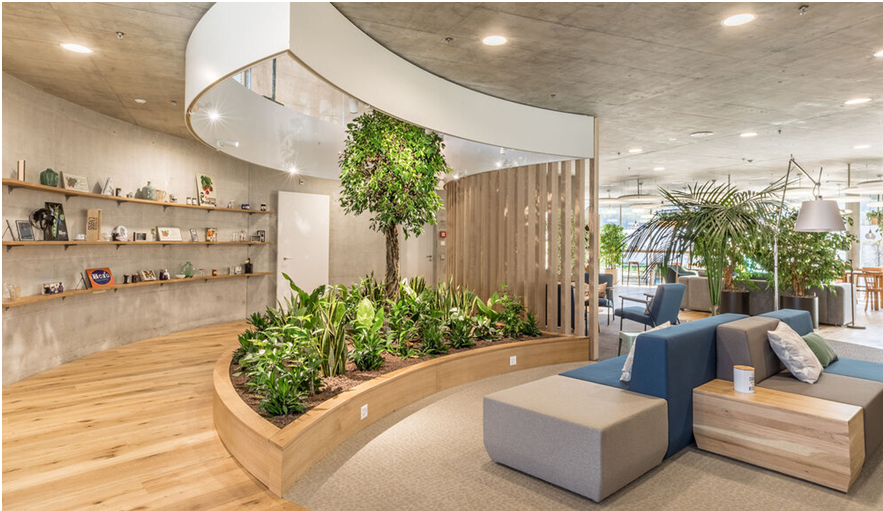
Its Energy Efficient
Image courtesy: Biofilico Design StudioWood is a fantastic thermal insulator when compared to both metal and concrete. In places around the country that depend on heating or cooling, wooden construction and framing directly translate into lower energy bills every month.
It’s Environmentally Friendly
From a raw material manufacturing perspective, using timber or CLT for construction is far kinder to the environment than concrete or steel. According to research conducted by Bimhow, a construction blog, the construction industry contributes to a staggering amount of pollution every year:
- 23% of air pollution & 50% of climatic change
- 40% of drinking water pollution
- 50% of landfill waste
If this is to change, switching to materials that are kinder to the environment during production and are sustainable to a larger extent than mining for limestone and iron ore is a positive step towards a greener future.
The Verdict
While it depends entirely upon the type of project, the growing popularity of wood as both a thriving wooden framing material and a construction staple is undeniable. With the spread of environmental awareness and the advancement of modern technologies, the future of wood is looking bright.